Overview
Foundation waterproofing requires continuity across systems. That's why we've brought together pre-applied and post-applied waterproofing into a complete, best-in-class system, including
Products & Accessories
Products
Sheet applied waterproofing
Sheet applied waterproofing
- Product Name
- Description
- Key Benefits
- Applications Type
PREPRUFE®250 pre-applied waterproofing membrane is a unique composite sheets comprised of a thick HDPE film, pressure sensitive adhesive and weather resistant protective coating.
- Forms a continuous adhesive bond to concrete poured against it
- Specifically designed to prevent water migration
- Continuous bond to poured concrete means PREPRUFE® 250 membrane is unaffected by ground settlement
- PREPRUFE® 250 is intended for low hydrostatic pressure or intermittent water conditions. Applications include construction such as garages, plant rooms and utility grade basements
Sheet applied waterproofing
Sheet applied waterproofing
GCP PREPRUFE® 275 and PREPRUFE® 275HC membranes are composite sheets made of HDPE film, a strong pressure-sensitive adhesive, and a weather-resistant coating.
- Forms a continuous adhesive bond to concrete poured against it
- Durable system designed specifically to withstand the force of shotcrete placement
Sheet applied waterproofing
Sheet applied waterproofing
GCP PREPRUFE® 300R/160R Plus pre applied waterproofing membranes are unique composite sheets comprised of a thick HDPE film, pressure sensitive adhesive, and weather resistant protective coating. Designed with Advanced Bond Technology™ and dual adhesive ZipLap™ seams, PREPRUFE® 300R/160R Plus form a unique, integral bond to poured concrete.
- The unique continuous adhesive bond to concrete poured against it prevents water migration and makes it unaffected by ground settlement beneath slabs
- Provides a barrier to water, moisture and gas physically isolating the structure from the surrounding substrate
- Easy roll/kick out installation reduces installation time and cost
- Release liner free, expedites installation and reduces construction site waste
- Simple and quick to install requiring no priming or fillets
PREPRUFE® 800PA post-applied waterproofing membrane works seamlessly with PREPRUFE® Plus pre-applied membrane to create a complete, fully integrated system for below-grade waterproofing.
- Aggressive Adhesion
- Superior Performance
- Fully Bonded
PREPRUFE® Detail Tape is a specially formulated, two-sided, highly aggressive tape. It is a 2 in (50 mm) wide x 50 ft (15 m) long self-adhesive tape with a release liner.
- Detailing accessory to the PREPRUFE® and PREPRUFE® SCS Systems
- Adhering HYDRODUCT® drainage composites and insulation boards to waterproofing membranes
PREPRUFE® Liquid Flashing is a two-component elastomeric, cold applied, trowel grade material designed for use with PREPRUFE® pre-applied waterproofing systems.
- Liquid applied
- Cold applied
- Waterproof
- Chemically cured
- System compatible
- Bonds to poured concrete
- Reduced labor
- Fillet material around pipe or rebar penetrations
- Sealing material at H-piles, columns, and terminations
- Damage repair of PREPRUFE® surface
PREPRUFE® SCS Plus System is a unique blindside waterproofing system specifically developed to provide a high performance waterproofing solution for shotcrete foundation walls.
Also acts as a methane barrier fully complaint to LARR requirement of LADBS AC-L137 for waterproofing and shotcrete.
- Post-injected grout fills and seals, providing ultimate waterproofing protection
- Aggressive bond to shotcrete resists lateral water migration
- Excellent resistance to hydrostatic pressure
- Applied vertically to timber lagging or other soil retention systems
PREPRUFE® Tape and PREPRUFE® CJ Tape are specially formulated two sided, reinforced pressure-sensitive tapes. These tapes are constructed with a highly aggressive adhesive which is designed to adhere to penetrations, protrusions and GCP waterproofing membranes.
- Highly aggressive pressure sensitive adhesive
- Weather resistant protective coating
- Form a continuous and integral seal to the structure
- Used in detail areas including end laps, penetrations and various tie-ins
- Used to patch damaged areas in the PREPRUFE® membranes
- Used at construction joints in concrete
Accessories
- Accessory Name
- Description
- Key Benefits
- Applications Type
PREPRUFE® Grout EG 75 is a high performance, solvent free, impermeable epoxy grout for maintaining the continuity of PREPRUFE® waterproofing systems at pile heads and similar structural penetrations.
- Compatible with all products in the PREPRUFE® sheet waterproofing system
- Impermeable
- High bond to substrate
- Rapid strength gain
- Waterproofing of pileheads and pilecaps
- Waterproofing of structural penetrations through PREPRUFE® waterproofing systems
- Recommended thickness range 1/2" (13mm) - 3" (75 mm)
The PREPRUFE® Tieback Cover is a specially designed, two-part cover used to maintain waterproofing integrity at soil retention tieback heads.
- Prevents water migration
- Fully-adhered watertight laps using PREPRUFE® Tape
- Simple and quick to install
- Easy to inspect
- Installed over cable and rod type tieback heads
PREPRUFE® Solved $4 Billion Transport Infrastructure Challenges
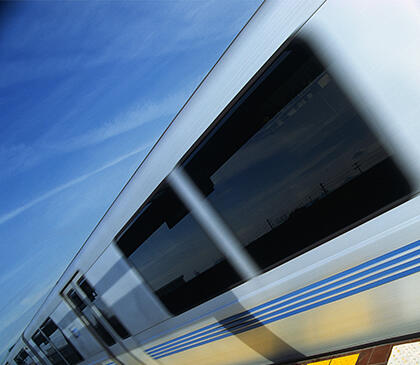
More Profiles
$2 Billion Power Plant Uses PREPRUFE® Below-Grade Waterproofing
We facilitated the waterproofing of a renewable energy manufacturing facility in Singapore
READ MOREArts Facility Use GCP to Complete Concert Design
New concert design implements an innovative waterproofing solution with our products.
READ MOREASB Tennis Centre Turns to BITUTHENE® Waterproofing Solution
BITUTHENE® 5000 essential to stadium construction
READ MOREAtalanta Sports Stadium Uses Full Waterproofing Solution
PREPRUFE® and BITUTHENE® membranes waterproof Italian sports center.
READ MORECrossrail Stations Gain Superior Waterproofing Solution
PREPRUFEⓇ waterproofs major UK construction project
READ MOREDoha Metro relies on PREPRUFE® Waterproofing
PREPRUFE® Plus waterproofing ensures dry metro stations with ease and reliability.
READ MOREEuropean Retail Complex Relies on PREPRUFE® Waterproofing
GCP protect one of the area’s largest retail projects from the roof to the vapor barriers
READ MOREGCP Waterproofs Cal Poly Recreation Center
The completion of the Cal Poly Recreation Center exceeds expectations after using PREPRUFE
READ MOREHeavy detailing no match for PREPRUFE® basement waterproofing
READ MORELas Vegas Airport adopts GCP waterproofing solutions
Using PREPRUFE®, BITUTHENE®, and HYDRODUCT® waterproofing solutions, the Las Vegas Airport
READ MOREMajor Commercial Building Succeeds with Premium Waterproofing
PREPRUFE® takes the worries out seawater damage in high performance, below grade foundatio
READ MOREMilan Metropolitan Underground Tunnel Relies on PREPRUFE®
PREPRUFE® used to waterproof 25,000 m2 of underground construction
READ MOREMultiple Waterproofing Solutions from One Source
Retail architects and developers turn to GCP to overcome complex waterproofing
READ MOREMuseum Construction Implements a Solution for Watertight Protection
PREPRUFE® and BITUTHENE® waterproofing utilized to protect 65€ million museum.
READ MOREMuseum of Islamic Art Built with Sustainability in Mind
High performance waterproofing of the foundation protects the finest collection of Islamic
READ MORENBA Stadium Lets It Rain with New Waterproofing
Stadium protected with PREPRUFE® Plus for below grade waterproofing
READ MORENew Estonia Museum Design Protects Cultural Artifacts
PREPRUFE® protects cultural artifacts with high performance waterproofing.
READ MORENewcastle Hospital Relies on GCP waterproofing
PREPRUFE® 300R and BITUTHENE® 3000 waterproofing protects UK hospital
READ MOREPREPRUFE® Waterproofing Protects Warsaw Spire Construction
Distinctive office project relies on watertight structural solution
READ MOREPREPRUFE® Waterproofing Protects Wembley Stadium
Wembley National Stadium gets waterproofing protection from the foundation to the roof.
READ MORESaudi Arabian Rail System Uses GCP Waterproofing Solutions
PREPRUFE® and BITUTHENE® waterproofing protect the Haramain Railway Stations
READ MORESubway Architecture Design in Seoul Calls for GCP Products
Seoul Subway utilizes PREPRUFE® 300R and BITUTHENE® 3000 to solve waterproofing issue
READ MORETuscany’s Apuano Hospital Chooses PREPRUFE® Waterproofing
Design and technical support help modernize Tuscany Hospital
READ MOREUtilizing ADPRUFE®, UK Shopping Center Opens on Time
Integrally waterproof concrete elements make the UK shopping center watertight.
READ MOREWaterproofing Solution Ideal for Cork Airport Expansion
Cork Airport Ireland utilizes GCP Technologies’ BITUTHENE® and PPREPRUFE® to protect again
READ MOREWaterproofing the $3.1 Billion Alaskan Way Viaduct
GCP provides mission-critical waterproof solution
READ MORERelated articles
briefcase
Click to find out more...
READ MOREBITUTHENE® Post-Applied Waterproofing
Overview A time-tested, field-proven product. Plaza decks, inverted roofs, green roofs and elevated decks. Basement walls. Tunnels, metro stations and infrastruct...
READ MOREPREPRUFE® SCS Plus Data Sheet
PREPRUFE® SCS Installation VideoProduct DescriptionPREPRUFE® SCS Plus is a unique blindside waterproofing system specifically developed to provide a high performance waterproofing solution for sh...
READ MOREWaterstops
Overview The way to a better waterstop Waterstops represent a critical component of any waterproofing system. Due to shrinkage and settling, the surfaces of a concrete cold...
READ MORE