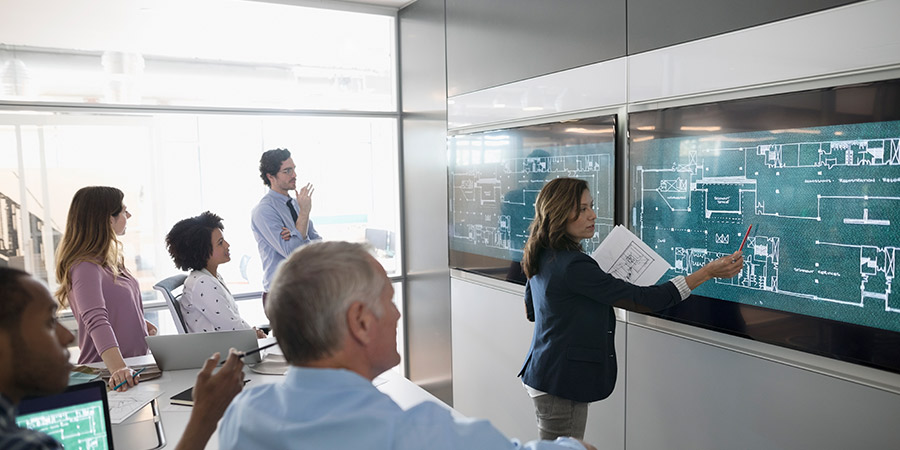
Delegated design—the process by which a principal architect, engineer, or for the sake of this discussion, a design professional of record (DPR) delegates certain structural elements to the contractor, sub-contractor, etc.—has been a topic of debate among the construction community. Especially if questions of liability arise when designed elements fail.
As long as design delegation continues to occur in traditional design-build and design-bid-build projects, and new project delivery approaches evolve, professional liability for the design of a project will find itself at the center of conflicts. This sometimes over-extended and potentially gap-filled method can confuse and redefine the traditional and expected relationship between the DPR and the builder.
Why delegate any portion of the design at all?
Construction is in a constant state of evolution. Increasingly complex products and systems hit the market all the time. It's the DPR's job to integrate the breadth of these diverse components into a single set of construction documents. This is no small task and has become increasingly difficult for the DPR to assume the role of a master builder, who can intelligently design systems and spec products across the entire project.
For more complex, more intricate systems, the DPR can delegate down to contractors or engineers with intimate knowledge of, for example, the precast parking garage adjacent to a building structure, or elevator support rails and beams.
Adapting to advanced building envelope technologies
The respective sciences of building envelope, fire protection and concrete technology have rapidly advanced in the recent past, as well. Construction assemblies today are more complex and include more material components. As a result, the number of transitions and interfaces between materials have also increased dramatically. These details require more knowledge and sophistication than ever before to execute system assemblies properly.
In these cases, the DPR essentially has two choices. They can delegate down the complex assembly of say, the building envelope, to the waterproofing contractors, requiring them to not only design these systems, but likely spec the multiple products involved. Or, the DPR can consult the manufacturer early in the design process.
In the latter instance, the manufacturer can come in and not only help specify the correct products, but also provide expert consultation on the assemblies of multiple products so that they work seamlessly together. The manufacturer should offer field support during installation of said systems, which is invaluable when ensuring complex systems are installed properly on the job. This approach also empowers the DPR to educate contractors when they dispute a particular design element.
Furthermore, engaging with your manufacturer early streamlines the entire design-build or design-bid-build process, from specification to installation. Responsibilities and, more importantly, communication are consolidated between all players on the project team.
Related articles
April 25, 2018
Streamlining international construction projects
An eye-opening Forbes article revealed international building projects that went billions over budget. Time and cost overruns are not uncommon in situations where stakeholders are working across count...
READ MOREMarch 07, 2018
Construction BIG DATA: Both grand and granular
Perhaps your construction business has hit a bit of a slump. Or maybe you’ve saturated a given market and would benefit from expanding into new territory. Unfortunately, in a climate that’s in constan...
READ MORENovember 09, 2017
Choosing the right project delivery process
When embarking on a new construction project, you have many choices when it comes to how the project is delivered. The different scenarios will impact the project timeline, costs, risks, and other fac...
READ MORENovember 09, 2017
A day in the life of a Design Advantage project manager
Design Advantage Project Manager Kimberly Shaw works closely with architects to help them simplify the design process. Today, we tagged along with Kimberly to learn more about her work. Can you tell ...
READ MOREOctober 23, 2017
Landing airport project on time
We're seeing an increasing number of clients interested in engaging with our Design Advantage team in the design process to help ensure project success. They're a group of highly-skilled construction ...
READ MORETags
- Architects
- Building Envelope Solutions
- Contractor
- Design Advantage
- Producer
- Subcontractor
- Waterproofing