X

Feb 11,2025
Saint-Gobain has completed the acquisition announced on June 27, 2024…
Jul 15,2024
July 15, 2024 – CHRYSO & GCP (Saint-Gobain Construction Chemicals…

Oct 27,2023
With urban space at a premium in the U.S., developers are finding it…
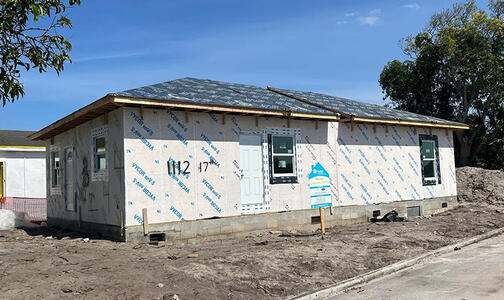
Jun 23,2023
It is no secret that the construction industry, like many industries,…
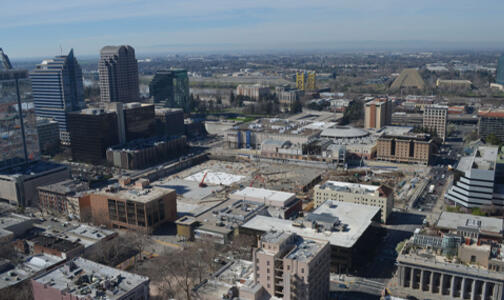
Jan 05,2023
With space at a premium in many urban areas, developers are digging…
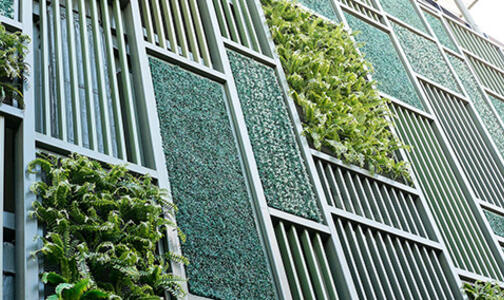
Oct 20,2022
The Inflation Reduction Act is aggressively tackling climate change…
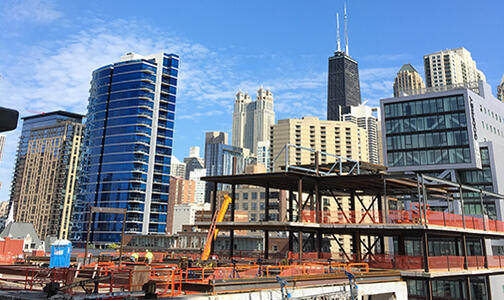
Aug 30,2022
No architect or building engineer today would consider erecting a…
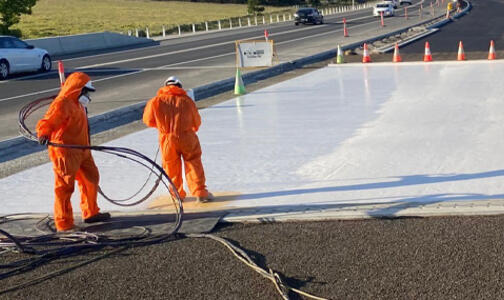
Oct 01,2021
When it came to selecting the waterproofing solution for bridge decks…

Feb 18,2021
Evaluating Liquid Waterproofing Membranes When it comes to…