With space at a premium in many urban areas, developers are digging deeper foundations to increase the square footage of high end residential, commercial and mixed-use building projects. The lack of above grade space is leading to increased use of basements for storage, archives, retail space and parking space. In other cases, a deep foundation may be needed due to large design loads or poor soil at shallow depths. In San Francisco for example, the Salesforce Tower is built on rock by way of cast-in-place foundations extending down approximately 265 feet.
Digging deeper foundations has many advantages, but also introduces many challenges that need to be addressed at the design phase, particularly for waterproofing. These challenges include:
Hydrostatic pressure. The soil around the foundation is generally saturated with underground water and or rain and this places immense hydrostatic pressure against the foundation. All of this pressure means that water will push its way through the foundation, even through miniscule cracks in the concrete. Where local hydrology allows, drainage systems can redirect some of the water away from the foundation, but they are generally not enough protection for concrete and finished basement space.
Corrosive groundwater. Digging deeper increases the chance of exposure to groundwater, which can have high concentrations of chlorides and sulfates in some regions. These conditions are highly corrosive to concrete. The structure can be protected from corrosion by using a waterproofing barrier that is resistant to aggressive soil/water conditions.
Dewatering. Depending upon geography and location of the project, water is often found when digging beyond 5 -10 feet. This requires continual dewatering measures to keep the site dry enough to construct the foundation. Dewatering involves running pumps 24x7, which is very expensive. To accelerate project completion and to minimize these costs, specialty building materials are available that are simple to install enabling concrete pours and basement finishing faster, helping to save time and money.
The Critical Mission: Specifying a suitable below grade waterproofing system
To overcome these challenges, specifying proven below-ground waterproofing during the design phase is critical. Waterproofing deeper basements, foundations and other below grade spaces takes special considerations that are vital to the life of the building.
A fully and permanently adhesive bonded, pre-applied waterproofing membrane offers the highest degree of protection in these deep foundation circumstances. By creating an integral bond with the poured structural concrete, the waterproofing barrier prevents water ingress, even at high hydrostatic pressure. Pre-applied waterproofing membranes, such as PREPRUFE® waterproofing system can even be placed in damp conditions, helping to accelerate project completion.
Building the new home of the NBA’s Sacramento Kings, The Golden 1 Center, for example, was complicated. The contractor faced the challenge of building an arena that would sit below the water table. In addition, the arena was being built adjacent to two major river systems, requiring a fail-safe below grade waterproofing solution.
To meet the requirements for operating dry, the contractors used PREPRUFE® Plus waterproofing system. The owners especially liked the fact that more than 650 million square feet of PREPRUFE® membrane have been installed worldwide on thousands of high-profile, must-not-fail projects. Today, the stadium continues to operate with no below grade leaks, in spite of extreme weather and a rising water table.
Building the new home of the NBA’s Sacramento Kings, The Golden 1 Center, for example, was complicated. The contractor faced the challenge of building an arena that would sit below the water table. In addition, the arena was being built adjacent to two major river systems, requiring a fail-safe below grade waterproofing solution.
To meet the requirements for operating dry, the contractors used PREPRUFE® Plus waterproofing system. The owners especially liked the fact that more than 650 million square feet of PREPRUFE® membrane have been installed worldwide on thousands of high-profile, must-not-fail projects. Today, the stadium continues to operate with no below grade leaks, in spite of extreme weather and a rising water table.
Designed with ADVANCED BOND TECHNOLOGY™ and dual adhesive ZIPLAP™ seams, PREPRUFE® Plus membranes form a unique, integral bond to poured concrete. This integral bond provides a robust barrier to water, moisture and gas and prevents both the ingress and lateral migration of water. The PREPRUFE® comprehensive waterproofing system has been protecting buildings like the The Golden 1 Center project across the globe for over 50 years and brings together pre-applied and post-applied waterproofing into a complete, best-in-class system.
As developers continue to face emerging challenges such as land shortages, they can utilize these locally available solutions to mitigate risk and protect the building’s design life while creating more usable space below the ground. There are many options available for below-ground waterproofing, but testing unproven solutions on these complicated deeper foundations can be catastrophic. It is mission critical to utilize proven systems that keep water out of basements, are backed by experienced technical support and innovative R&D, as well as hold a state of the art manufacturing track record.
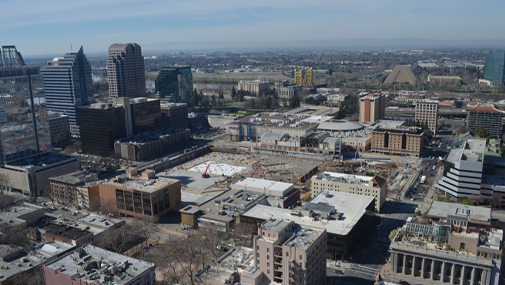
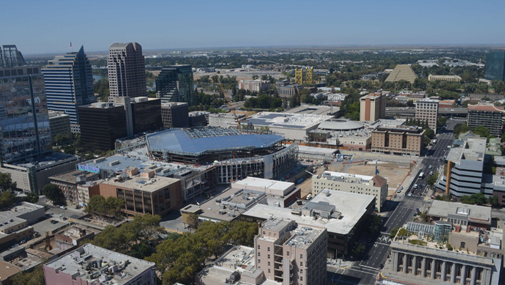