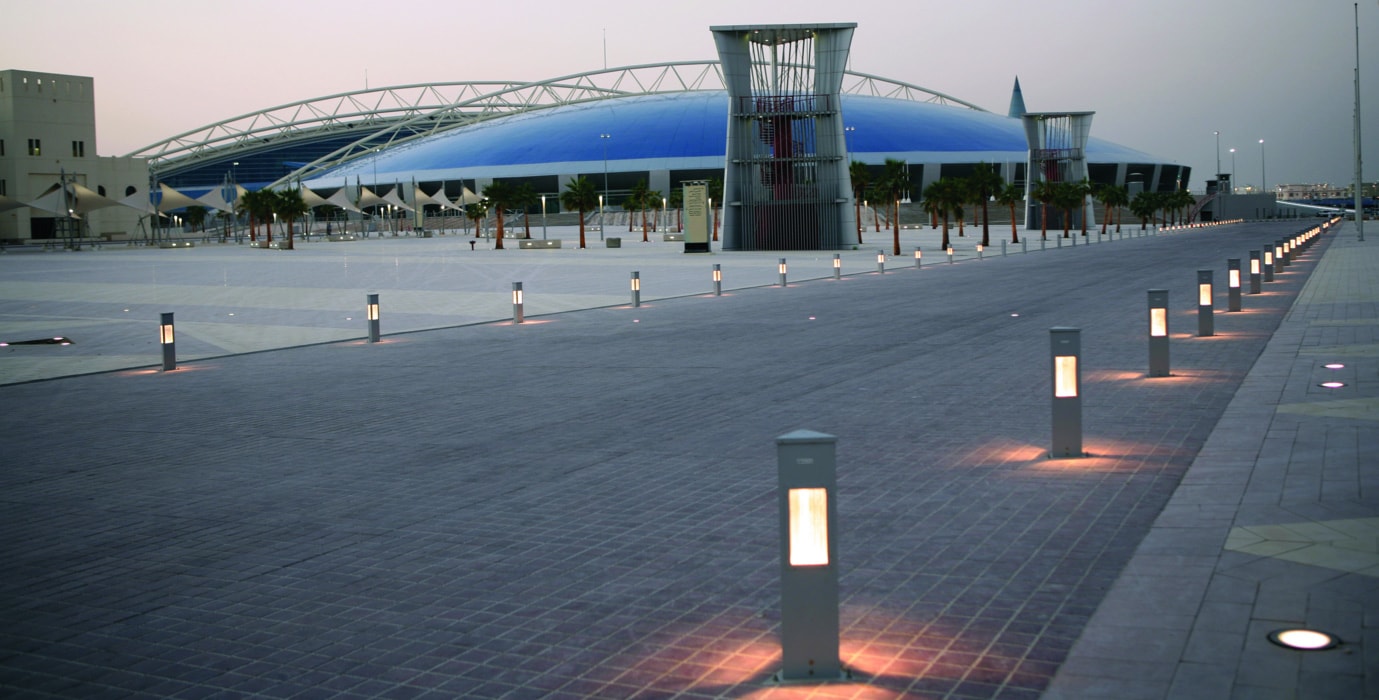
Hundreds of concrete buildings are under construction in the Middle East. Yet how do construction crews protect them against the ravages of a blistering desert climate? Iltaz Alam, building envelope expert for GCP Applied Technologies, provides some answers.
The Middle East is seeing a construction boom with more than a trillion in USD of major projects planned for completion by 2030, Alam said. As durable as concrete is in below grade applications, the conditions in the region present a severe test for the material.
Concrete challenges in a Middle Eastern climate
- Extremes of seasonal and daily temperature
- Wide range of ambient humidity and moisture from hot humid exteriors to air-conditioned interiors
- Chlorides and sulfates in the groundwater
Without the protection offered by a high performance waterproofing membrane, concrete is vulnerable to structural deterioration in such aggressive conditions. Chemical, UV, and mechanical damage can all compromise a system’s effectiveness. When specifying a below grade waterproofing system it’s crucial to consider how resistant it is. It's especially important when results range from stress cracks to total flooding which can be astronomically expensive.
Rebar corrosion is a significant issue for reinforced concrete structures in the Middle East, with chloride ingress through airborne salts or below grade chlorides and sulphates acting as the most frequent cause. In hotter climates, the process is faster with every extra 10°C doubling the rate of diffusion. As the steel corrodes, the concrete cracks, making the problem worse. Full protection can only be achieved using a physical barrier to water infiltration such as a chemically resistant bonded waterproofing membrane.
Well-performing projects
Products and materials are expected to deliver long-term performance for new buildings and civil engineering projects in the Middle East, many of which are being delivered with a service life of 100+ years.
The multi-billion dollar Doha Metro Rail system in Qatar is no exception. It saw the specification of more than 1,000,000 m2 of high performance PREPRUFE® pre-applied below grade waterproofing system to protect against groundwater, with a 120-year design life.
Another rail project, this time linking the holy cities of Saudi Arabia, the Haramain High Speed Railway had the challenge of building four new stations in just four years, in extreme heat and desert conditions. PREPRUFE® 300R waterproofing membrane was selected to provide exceptional protection to all built elements below and above the water table.
The Preprufe advantage
Workmanship is essential in achieving a durable structure. Concrete and membrane installation must be supervised by qualified and experienced personnel. Systems which minimise installation risk, therefore, are highly beneficial in tough desert conditions.
With its single layer adhesive application directly to wet or dry cement, PREPRUFE® creates an impenetrable seal and offers simple and efficient detailing. It reduces the risk of human error in installation, it saves time, requires few ancillary products and reduces cost of site supervision.
Every new construction project in the Middle East is vital to the region’s continued growth and development. The impact of any failure is significant. Specifying a waterproofing system that is proven to cope with the climate’s demands is an absolute must for a long and reliable service life.
For more about the full range of PREPRUFE® products visit preprufe.com. For general enquiries including technical, on- or off-site support, please email preprufe@gcpat.com.
Tags
- Concrete
- Mass transit
- PREPRUFE
- Transportation Infrastructure
- Underground Solutions
- Water stop
- Waterproofing